FlightMetals Reveals Properties of Nickel Alloy AMS 5663
Dec 15, 2022
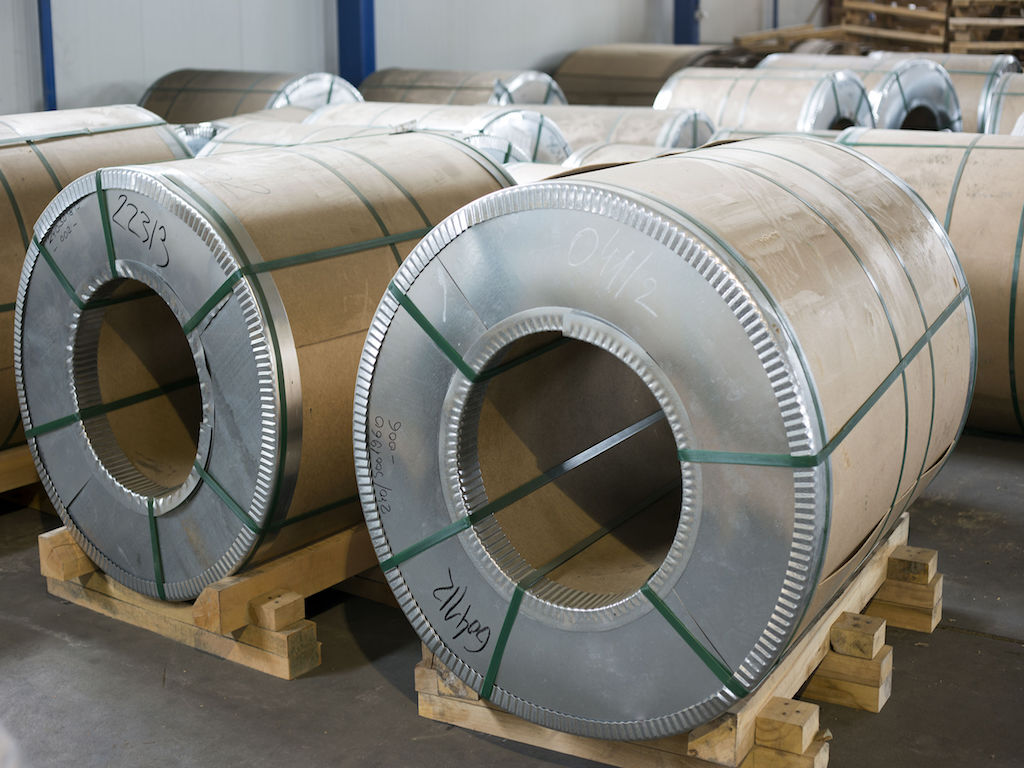
Nickel based super alloy AMS 5663 (also called Inconel 718) is especially well suited for use in high temperature environment where corrosion, creep and thermal shock resistances are demanded. This alloy is perfect for aerospace industry due to its hardness and favourable properties and features.
The Real Super Nickel Based Alloy - AMS 5663 is considered as the real super nickel based alloy with the ability to be used permanently above 600°C. Its Young's modulus is approximately double than of Ti6Al4V and close to that of an unalloyed carbon steel (CK 45). This super alloy holds better rupture and creep strength with high resistance to fatigue and corrosion. It maintains strength and toughness over a long period of time at high temperatures with corrosion resistance ability at high temperatures.
AMS 5663 (Inconel 718) covers about 50% of the aircraft turbojet engines’ weight, being the prime component for blades, discs and casing of the high pressure section of the discs and compressor as well as some turbine section’s blades. It also has some applications in cryogenic environments and rocket engines as it has good toughness at low temperature (protecting parts from brittle fracture).
AMS 5663 (Inconel 718) highly contains iron which lowers its cost per kilogram while providing it a precipitation hardening effect. In the matrix, low mobility of iron gives the main strengthening phase (γ’’) a slow precipitation kinetics that lowers susceptibility to post-weld cracking. Inconel 718 is designed to overcome the low joinability of this materials’ class, typically susceptible to crevices (microstructural segregation of alloying components in the heat-affected zone of welds).
Some alloying elements provide AMS 5663 an extreme resistance to corrosion up to 1000°C / 1832°F. For example, nickel is helpful in fighting with chloride stress corrosion cracking (CLSCC) and protects from corrosion in many organic and inorganic oxidizing compounds, in a wide range of alkalinity and acidity. Chromium gives this alloy the ability to handle the attacks from oxidizing media and sulfur compounds while Molybdenum help in improving resistance to pitting corrosion.
Two strengthening modes are combined: solid solution hardening (atoms of iron, chromium, molybdenum and niobium can substitute to nickel within the metallic matrix) and hardening by a precipitation of ordered intermetallic phases, γ' and γ'’. Precipitation of the intermetallic phase γ', Ni3(Ti, Al), forms titanium and aluminium, which are metastable and re-hardenable from solid solutions of niobium and titanium (at room temperature) and molybdenum or tungsten (at higher temperatures). At the temperature around 650°C, niobium combines with Nickel by precipitation the γ'' phase (Ni3Nb), which has high mechanical properties at moderately high and very low temperatures. Although γ’’ and γ´ are existing in the aged condition, the amount of γ´ is very small and γ’’ is considered as the primary strengthening agent. The precipitates of γ'' are disc shaped, with the thickness of 5-9 nm and an average diameter of around 60 nm.
FlightMetals can offer you the top quality nickel metal AMS 5663 at best price that you would expect from a premier specialty metal supplier.